Voltage imbalances between ground and neutral conductors represent a crucial issue in the field of industrial electrical installations. This phenomenon, characterized by the occurrence of unexpected potential differences, can significantly compromise both the integrity of electrical systems and the operational safety of industrial plants.
The most evident manifestation of this condition is the presence of return currents through the ground, a scenario where part of the load current deviates through the protective conductor instead of returning exclusively through the neutral. This not only undermines the fundamental principles governing a safe and efficient electrical design but also opens the door to a series of potential risks.
The severity of this problem lies not only in its potential to generate energy losses and damage expensive equipment but also in the risk it poses to personnel safety and operational continuity. Voltage imbalances between ground and neutral can cause issues ranging from subtle inefficiencies to catastrophic failures, including interference in control and communication systems, accelerated wear of electrical components, and in extreme cases, fire or electrocution hazards.
To better understand how to address this issue, it is crucial to identify its main causes:
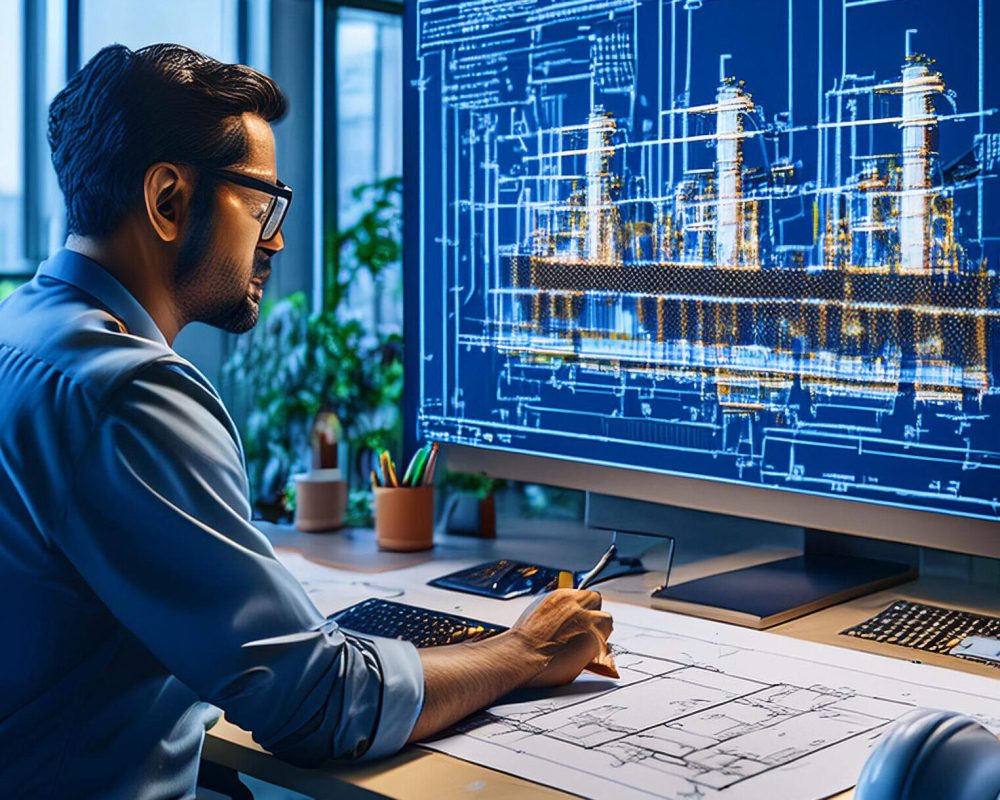
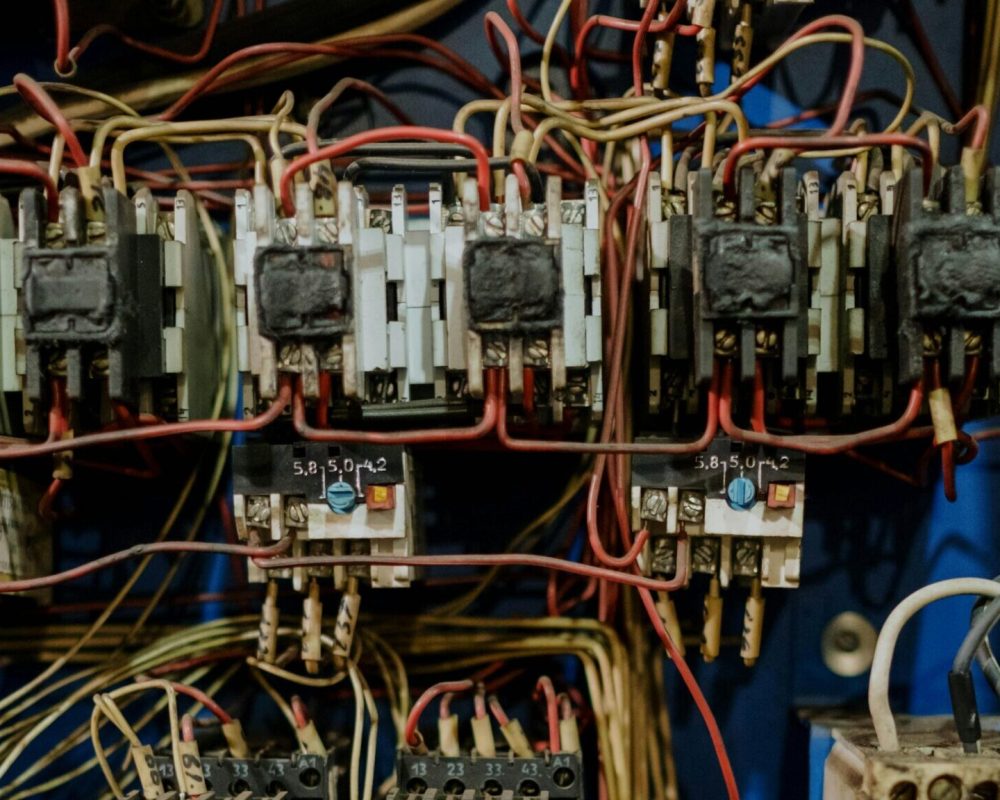
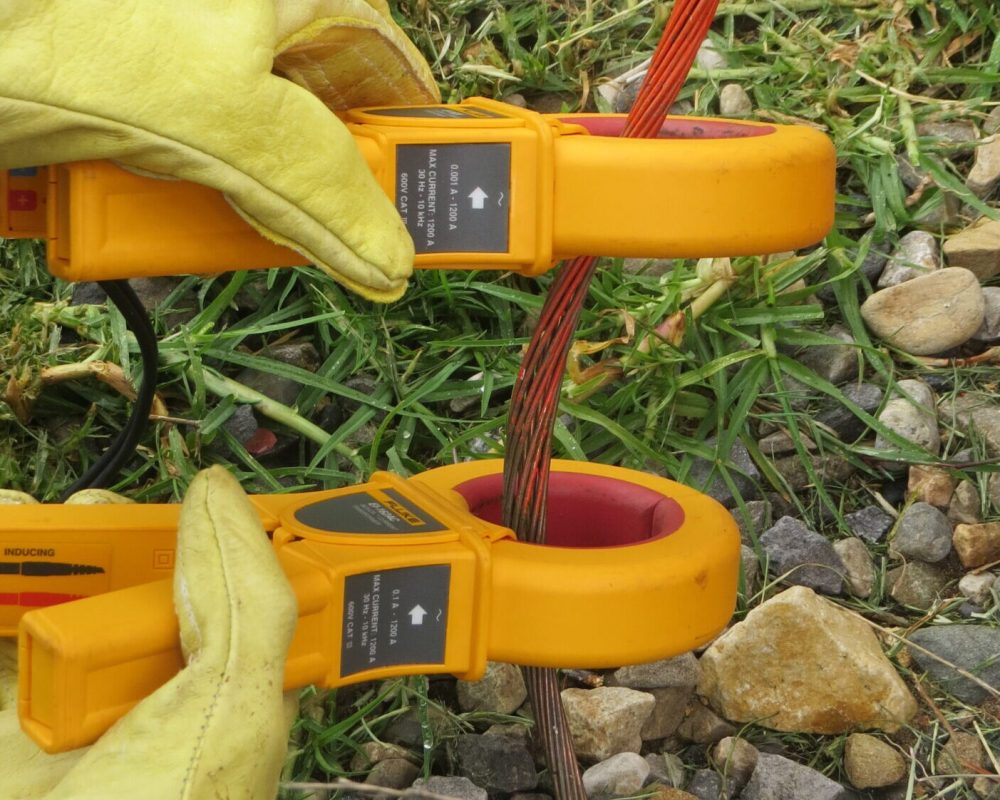
Errors in grounding system design:
Frequently, the importance of a robust equipotential network is underestimated, resulting in systems inadequate for managing electrical loads and mitigating electromagnetic disturbances present in industrial environments.
Irregularities in the construction phase:
Failures in executing unions and connections of protective conductors are particularly critical, as they can introduce high impedance points in the system and compromise its effectiveness.
Deterioration of the system due to lack of preventive maintenance:
Over time, the system’s integrity can be compromised, resulting in gradual increases in impedance at critical points in the grounding circuit, which diminishes its protective capacity.
To address these issues, the following solutions are proposed, categorized by the three main causes or stages of the project:
Electrical Installation Design:
a) Implement a mesh grounding system with multiple connection points, reducing the overall impedance of the system.
b) Oversize protection and neutral conductors, anticipating possible increases in future loads.
c) Integrate continuous monitoring systems for leakage currents, allowing early detection of anomalies and parametric deviations.
Electrical Installation Construction:
a) Adopt exothermic welding techniques for all critical connections in the grounding system, ensuring low impedance and high durability joints.
b) Implement a rigorous protocol for verifying the continuity and resistance of connections, thoroughly documenting the results and traceability.
c) Install physical barriers to protect ground conductors from mechanical damage, especially in high-traffic or exposed areas.
Electrical Installation Maintenance:
a) Establish a program of periodic measurements of the resistance of the grounding system and equipotential bonds, with frequencies adapted to the specific operating environment.
b) Conduct regular thermographic inspections to detect hot spots in connections, indicative of anomalous resistances or component degradation.
c) Implement a system for recording and tracking ground fault events, enabling long-term trend analysis and proactive identification of problem areas.
The effective management of industrial electrical systems requires a comprehensive and dynamic approach. By systematically addressing the imbalances between ground and neutral, from the initial design to continuous maintenance, not only is operational safety improved, but the overall plant performance is optimized. This proactive strategy translates into greater equipment longevity, a significant reduction in downtime, and an increase in energy efficiency.
As professionals in the sector, our fundamental role is to stay at the forefront of best practices, implementing innovative solutions and adapting to changing technological demands. In doing so, we not only protect the facilities we oversee, but also drive the evolution of the entire industry towards higher standards of excellence and sustainability.
At Voltia, we have a team of Engineering and Technical Operations professionals to assist in the safe management of industrial electrical infrastructure and minimize the impact of this type of situation. For more information, please write to info@voltia.com.co, describing your case, and our expert team will show you the best alternatives for smart and safe management of your electrical infrastructure.